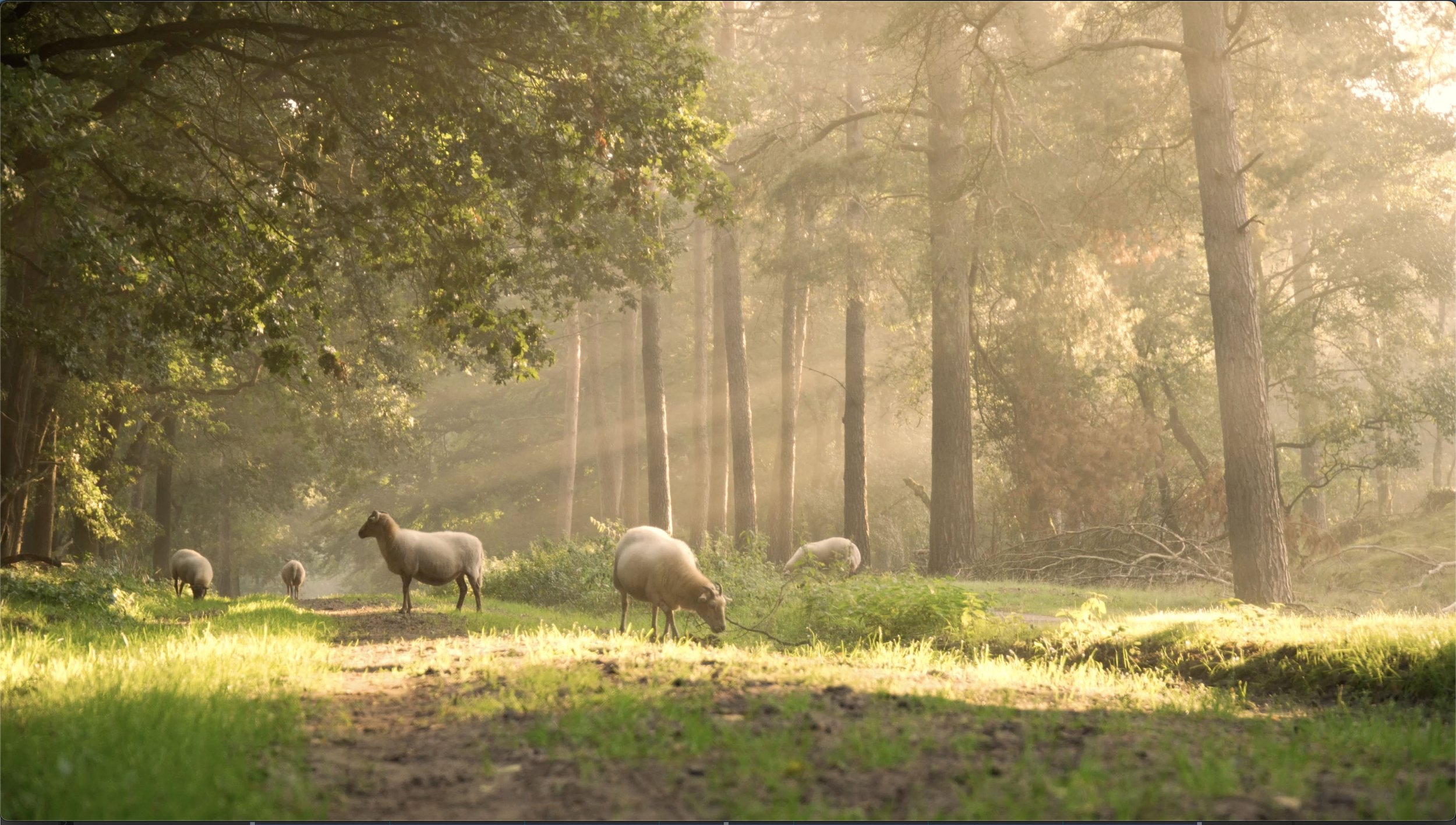
Would you believe me if I told you that
manufacturing sustainable footwear is really easy?…
-
Who
It is actually very simple to manufacture sustainable footwear.
In fact I can do it with pure natural and renewable materias and techniques already known.
No fossil oils, no plastic, no animals hurt and no CO2-”footprint” except from what is used transporting the materials and finished products.I have been working with woolen felted shoes for more than 20 years, and it is several years since I figured out how to modernize the whole concept of footwear manufacturing.
I am inviting customers/investors/partners in order to reach a yearly production of 30.000 pairs or more, I will then build a new production facility that can scale infinitely and slash down the cost of production..So, the entry barrier for this business is not that high. However I have raised it with a patent. Thus the profit will be higher the sooner any investor chips in.
My experience counts three attempts, 3 previous production units in Denmark, Romania and Nepal, almost 100 employees, launching brands from scratch and raising funds from several investors. I have of course made a lot of mistakes, and more is likely to come, so this time I want persistent partners who is in it for the cause and not only for the money.
-
What
It really is simple!
To make beautiful and super comfortable footwear of natural and sustainable materials without causing harm to our environment.The first material is wool for the upper.
We want a light weight and hardwearing material that is soft anf comfortable to wear on our bare skin.
Wool is natures way of dressing the animals for both winter and summer. It is abundant and renewable without any need to kill the source.
It is able to absorb a lot of moist and it easily release it again. On top of this a natural content of lanolin protects it from dirt and odors.In fact we have known this for centuries. Just mind the russian valenkies (Woolen Felted Boots) that helped their soldiers withstand the harsh winters.
Some brands are already using woolen uppers. Several home shoes are manufactured from cocked or felted wool. Very few are offering anything but indoor shoes, since the production techniques are old and limits the range of designs. Especially Allbirds have done a great job, solving this problem by knitting the upper and I am sure more will follow. But, it can be done even better with the gain of more comfortable footwear for less cost
The second material is natural rubber for the soles..
Mold injected soles have gone through a wonderful development in this last decade. However I have wondered why they are all done in plastic and carbon based rubbers, when using natural rubber offers so many opportunities and so low costs for tools.
-
How
Making a woolen shoe is in fact really simple.
Make a woolen sock, fill in a last and shrink the wool around the last. Mount a sole after that and you have an extremehy comfortable and habit-forming shoe.
The shrinking/felting can be done by hand or it can be mechanized.
My dear mother invented a simple way of industrializing the process and this is in various ways the common way to manufacture today.
Felting by hand is of course very labour intensive so for mass production you need an industrialized technique.
One skilled worker at my workshop in Kathmandu can manufacture 2 - 3 pairs a day. On a modern facility a workers output will be around 20 pairs a day. I want to at least double this productivity. Since labour cost makes up half the expenses, and In all fairness, paying less for the labour is not the solution, productivity will have to be raised in order to bring down the cost of production.
To do this I have made a plan. Klick here if you want to know my plan and maybe buy some woolen shoes or even join my project.